La operación de conformación en frío consistente en la reducción de sección de un alambre o varilla haciéndolo pasar a través de un orificio cónico practicado en una herramienta llamada hilera o dado.
PROCESO:
Las diferentes operaciones que se realizan durante este proceso son:
-Patentado: Tratamiento térmico que consiste en calentar el alambre hasta 950ºC, y una vez alcanzada dicha temperatura; enfriarlo bruscamente en un baño de plomo a 500ºC. Este tratamiento tiene por objeto dar al alambre una estructura dúctil que permite el trefilado
-Decapado. Consiste en preparar y limpiar el material, eliminando el óxido que puede haberse formado en las superficies del material, en laminaciones anteriores. Normalmente se hace mediante ataques químicos y posteriormente se realiza una limpieza con agua a presión.
-Trefilado. Los lubricantes y diferentes máquinas son los factores principales. Se suele utilizar de lubricantes la parafina y el grafito en solución coloidal o finamente dividido.
-Acabado. Una vez que ya ha salido el material de la hilera, se le somete a operaciones de enderezamiento, eliminación de tensiones y, a veces, algunos tratamientos isotérmicos para conseguir mejoras en las características mecánicas del producto.
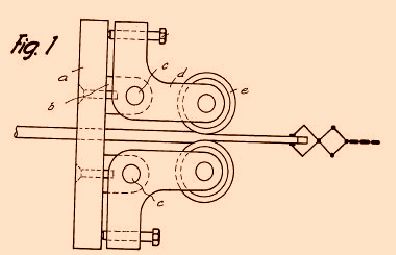

Extrusion:
In extrusion, the workpiece is placed in a container and compressed until pressure inside the metal reaches flowstress levels. The workpiece completely fills the container and additional pressure causes it to travel through an orifice and form the extruded product.
Extrusion can be forward (direct) or backward (reverse), depending on the direction of motion between ram and extruded product. Extruded product can be solid or hollow. Tube extrusion is typical of forward extrusion of hollow shapes, and backward extrusion is used for mass production of containers.

c-tube extrusion; d-container extrusion.
Piercing is closely related to reverse extrusion but distinguished by greater movement of the punch relative to movement of the workpiece material.
Secondary Processes Besides the primary forging processes, secondary operations often are employed. Drawing through a die is a convenient way to eliminate forged draft. The mode of deformation is tangential compression. The diameter of the drawing ring can be slightly smaller than the outer diameter of the preforged shell to control or reduce wall thickness and increase the height of the shell in a drawing or ironing operation.
Bending can be performed on the finished forging or at any stage during its production.
Because forging stock may assume complex shapes, it is rare that only a single die impression is needed. Preforming the forging stock--by bending or rolling it, or by working it in a preliminary die--may be more desirable. Gains in productivity, die life, and forging quality often outweigh the fact that preforming adds an operation and attendant costs. Forging in one final die impression may be practical for extremely small part runs.

b-ironing
Since bending of larger parts requires a machine of long stroke, special mechanical or hydraulic presses are often necessary. Simple shapes can be bent in one operation, but more complex contours take successive steps. If complex shapes are to be formed in a single operation, the tool must contain moving elements.
Special Techniques After deformation, forged parts may undergo further metalworking. Flash is removed, punched holes may be needed, and improved surface finish or closer dimensional accuracy may be desired.
Trimming-- Flash is trimmed before the forging is ready for shipping. Occasionally, especially with crack-sensitive alloys, this may be done by grinding, milling, sawing, or flame cutting.
Coining--Coining and ironing are essentially sizing operations with pressure applied to critical surfaces to improve tolerances, smoothen surfaces, or eliminate draft.
Coining is usually done on surfaces parallel to the parting line, while ironing is typified by the forcing of a cup-shaped component through a ring to size on outer diameter. Little metal flow is involved in either operation and flash is not formed.
Swaging--This operation is related to the open die forging process whereby the stock is drawn out between flat, narrow dies. But instead of the stock, the hammer is rotated to produce multiple blows, sometimes as high as 2,000 per minute. It is a useful method of primary working, although in industrial production its role is normally that of finishing. Swaging can be stopped at any point in the length of stock and is often used for pointing tube and bar ends and for producing stepped columns and shafts of declining diameter.

valve body.
Hot Extrusion-- Extrusion is most suitable for forming parts of drastically changing cross section and is, therefore, a direct competitor to continuous upsetting and the horizontal forging machine. In a bar section of car efully controlled volume is heated, descaled, and placed into the die. Under pressure of the closely fitting punch the material first fills the cavity, then part of it is extruded into a long stem. At the end of the stroke, a valve body is obtained that needs only grinding of the seating surfaces.
There are a number of variants of the extrusion process, many of them patented. The slug may be hollow (machined), pierced in a separate operation or in the extrusion process itself. In all instances, the quality of heating, the efficiency of scale removal or prevention, and the effectiveness of lubrications are matters of greatest importance. The variety of shapes produced are numerous. Dimensional accuracy, surface quality, and productivity are high, and a greater degree of deformation can be achieved in a single operation than in any other forging method.
Cold, Warm, and Hot Forging--What's the Difference?Cold Cold forging involves either impression die forging or true closed die forging with lubricant and circular dies at or near room temperature. Carbon and standard alloy steels are most commonly cold-forged. Parts are generally symmetrical and rarely exceed 25 lb. The primary advantage is the material savings achieved through precision shapes that require little finishing. Completely contained impressions and extrusion-type metal flow yield draftless, close-tolerance components. Production rates are very high with exceptional die life. While cold forging usually improves mechanical properties, the improvement is not useful in many common applications and economic advantages remain the primary interest. Tool design and manufacture are critical. Warm Warm forging has a number of cost-saving advantages which underscore its increasing use as a manufacturing method. The temperature range for the warm forging of steel runs from above room temperature to below the recrystallization temperature, or from about 800 to 1,800°F. However, the narrower range of from 1,000 to 1,330°F is emerging as the range of perhaps the greatest commercial potential for warm forging. Compared with cold forging, warm forging has the potential advantages of: Reduced tooling loads, reduced press loads, increased steel ductility, elimination of need to anneal prior to forging, and favorable as-forged properties that can eliminate heat treatment. Hot Hot forging is the plastic deformation of metal at a temperature and strain rate such that recrystallization occurs simultaneously with deformation, thus avoiding strain hardening. For this to occur, high workpiece temperature (matching the metal's recrystallization temperature) must be attained throughout the process. A form of hot forging is isothermal forging, where materials and dies are heated to the same temperature. In nearly all cases, isothermal forging is conducted on superalloys in a vacuum or highly controlled atmosphere to prevent oxidation. |
No hay comentarios:
Publicar un comentario